A survey by Intuit revealed that more than two-thirds of employees who GPS had tracked indicated that it’s one of the most compelling benefits they see from a safety perspective. An IIoT Personnel Tracking System (PTS) has proven to contribute to employee safety in harsh and dangerous workplaces like mining and petrochemical factories. “Worker Safety” is an organization’s shared responsibility with its employees irrespective of the workplace, duties, priorities, roles, and activities of everyone. Personnel Tracking is not perceived as a breach of Worker Privacy. 7 out of 10 employees feel risk-free and safe when tracked at work. An effective RTLS contributes to this enterprise endeavor in many organizations today.
In this light, greater accuracy, accountability, and tracking mileage have contributed to the increased usage of RTLS for employee tracking in the workplace. According to Intuit’s recent survey, 64% of employees using GPS for personnel tracking have experienced better workplace safety than the others during emergencies and hazardous conditions.
The Tracklynk Personnel Tracking System (PTS) enables enhanced personal safety for hazardous-workplace employees with its Preemptive, Situation Awareness, and Responsive (SAR) capabilities. RTLS can improve some of the workplace safety protocols that benefit employees and reduce security breaches in the following ways:
Critical Alerts
These systems provide life-saving alerts when:
- Dangerous levels of toxic fumes and gases are detected.
- Accumulated levels of fumes are reached per shift.
- A Designated Dangerous Area Geo-Fence is Crossed.
- A Muster or Evacuation is called.
Such alerts allow managers to quickly get a headcount and locate all the employees to expedite rescue efforts based on a reliable ‘all accounted for’ check.
Alerts to designate OSHA Safety Warden or Company Site Manager
As per the guidelines set by the Occupational Safety and Health Administration (OSHA), one emergency warden should be allocated for every 20 employees. These wardens are responsible for checking the workplace during an evacuation as the last person to leave during an emergency. Additionally, this person needs to ensure that employees assemble at the mustering (or safe zone) area. The Site Manager can be alerted to potential safety hazards and locations to take preventive action.
These systems also help intelligently detect when and where an employee:
• Falls or is “man down.”
• Struck or has encountered an accident.
• Breaches a Geo-Fenced area.
• Is “unaccountable.”
Access Control and Geofencing
Not only do access control systems aid in the emergency management and mustering process, they even protect your facility from unauthorized access.
ACS helps detect the following:
• Employees on active duty.
• Average zone efficiency.
• Social distancing incidents (during COVID-19).
• Total visitors
• SOS incidents
• Unauthorized Movements.
• ID card not attached to an employee.
In a facility, there would be areas restricted for employees like data rooms or administrative regions. Facilities could also contain hazardous materials such as chemicals or machinery that should be off-limits to unauthorized people. Some premises also have gates or doors that are unsecured. With layered protection, access control can be customized based on your facility and employee needs and time of day access parameters. In addition, site managers can also log access control data if they need to determine who accessed a specific area of your facility. Workplace geofencing triggers prompt employees to clock in and out using an authorized ID or device to enter or exit a job site. This ensures that only authorized personnel uses a facility while unauthorized access raises an alert through anomaly detection. Natural disasters such as tornadoes and wildfires can happen at any time, posing a significant threat to your employees’ lives and your facility. Likewise, such emergencies and manufactured disasters like fire or toxic explosions can prompt immediate evacuation or shelter-in-place scenarios. OSHA requires every establishment, small or large, to have site-specific employee emergency response plans, clear evacuation plans, marked fire exits, and mapped routes. In addition, workplace safety requires systems and training to ensure employee readiness. Incident emergency response planning includes developing, training, and implementing an incident command structure to ensure a safe and coordinated emergency response. The RTLS technology is now being incorporated into emergency management plans across industries for which an evacuation route and safe mustering location (safe zone) are fundamental. PTS provides clinical-grade visibility for emergency employee tracking where first-responders can respond immediately and efficiently with knowledge of any missing employee.
The features of RTLS-based emergency management include:
Sensors for Alerts: Set automatic alerts that trigger various actions or events. Sensor alerts help track the temperature, smoke, gas, and more.
Actions for Alerts: Actions can include sending messages (SMS or Email) and activating relays such as sirens, gates, lights, sprinklers, etc.
Traceability:
- Non-arrival alerts can be set to notify or trigger an action when someone is not at a specific pre-defined zone or mustering location.
- Management of High-Security areas is addressed with pre-defined areas for specific personnel only.
Other Benefits of RTLS asset tracking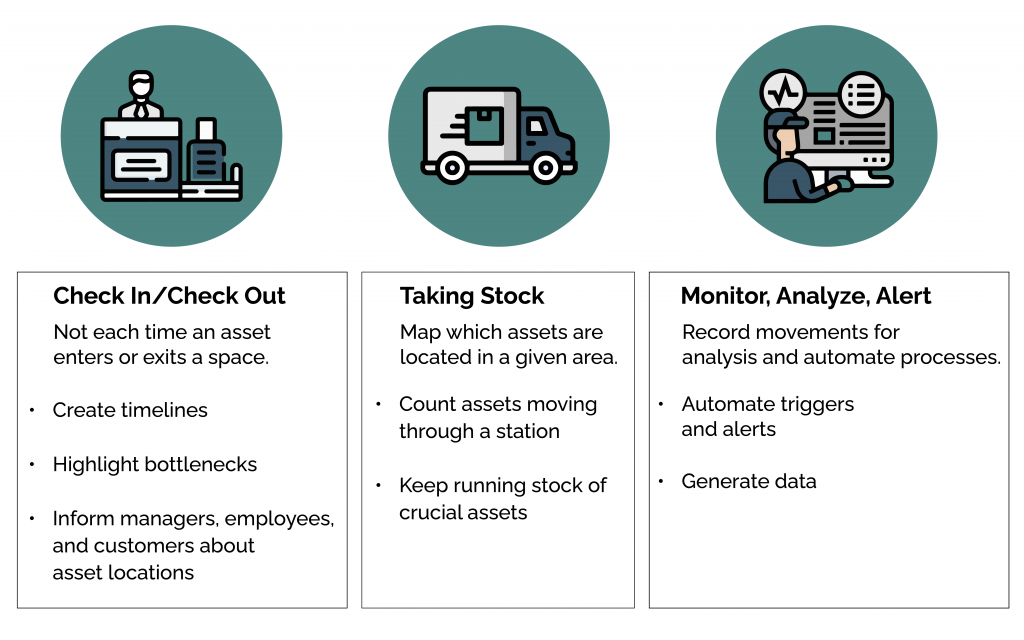
- Automate inventory control: RTLS helps with inventory automation which is labor and time-intensive and expensive otherwise.
- Real-time reporting: RTLS tagging helps with accurate reporting and optimizing your supply chain.
- Asset management: Increase asset visibility, location accuracy, and update speed to maximize supply chain productivity, value, and deployment ROI.
- Yard management: Intelligently track critical worksite equipment when you need it most.
Are you looking to implement a customized PTS and RTLS Safety solution in your organization? Then, you’ve come to the right place. Let’s connect to explore the opportunities!